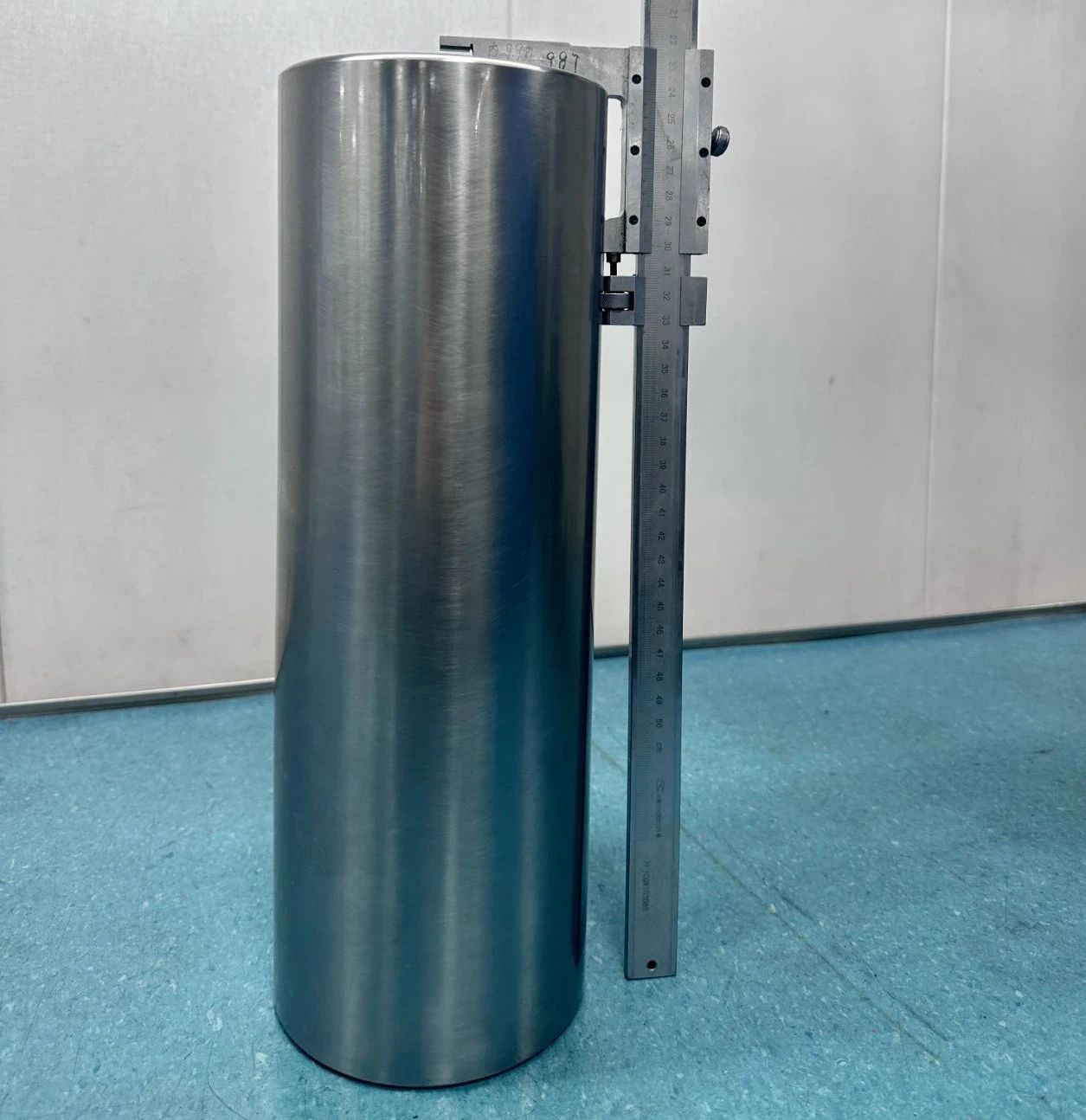
Recently, Luoyang Huigong Bearing has successfully developed another super-large tapered roller, which has successfully passed the customer's on-site acceptance.
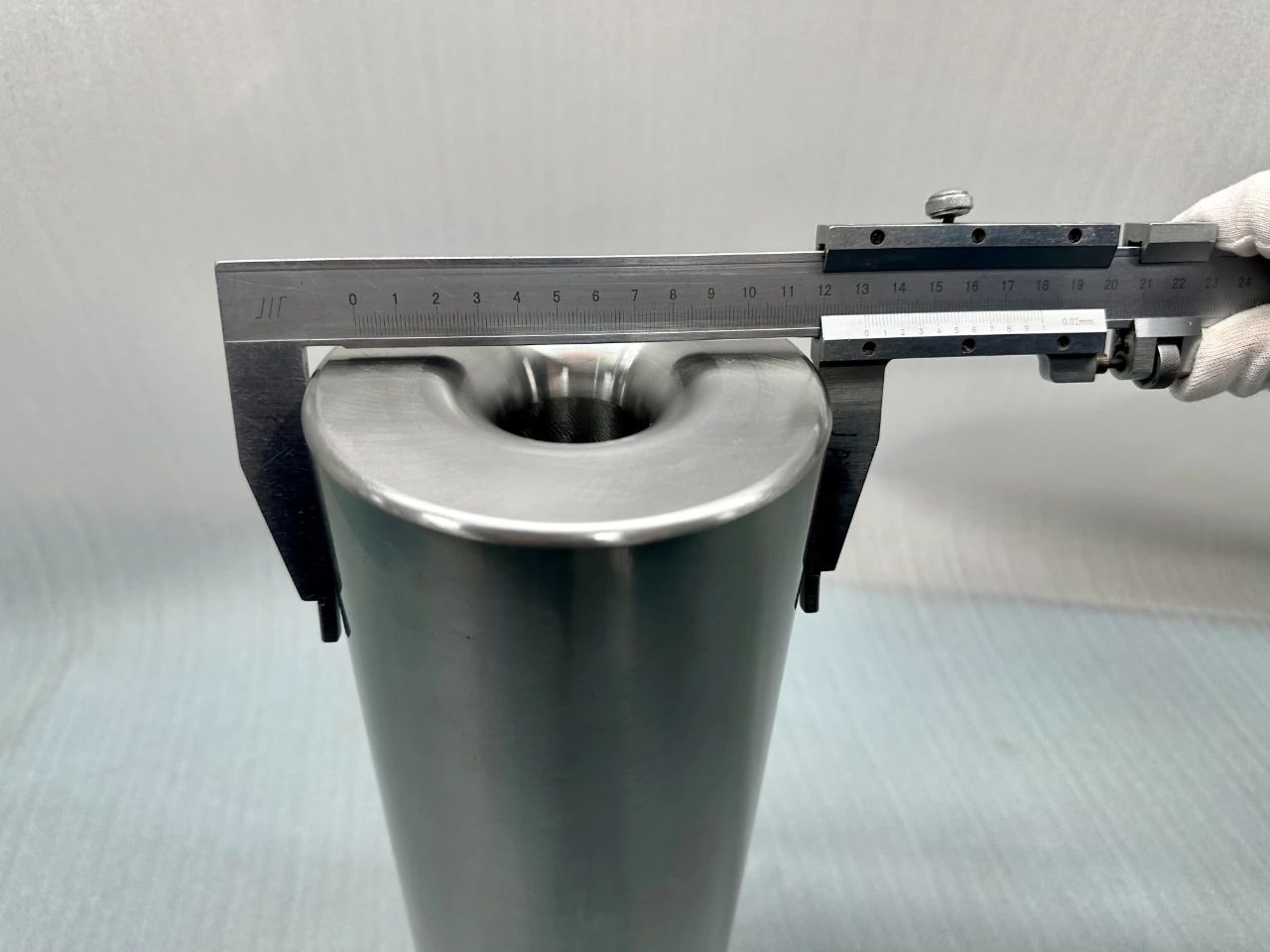
In mid-October, the company received a trial production order for the processing model FD-306/3250/P5/04 roller. This wind turbine roller TRBΦ132*370mm, with a deadweight of 33.7kg, is the largest and most difficult to process roller currently in production, and is suitable for the main shaft bearings of the largest wind turbine equipment currently.
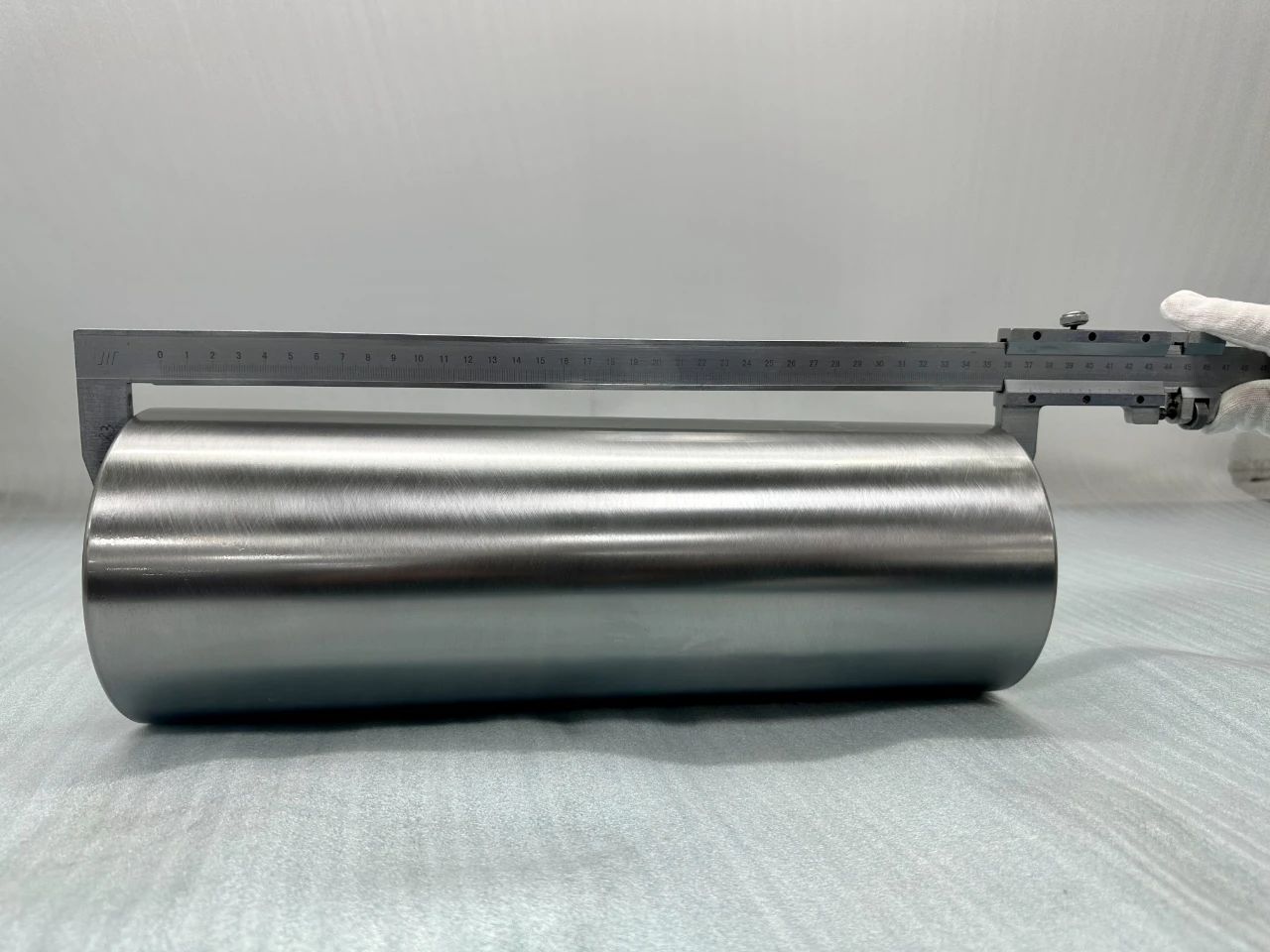
During the research and development process, the customer's technical drawings required that the three points of the busbar length vertex, the maximum measurement point and the maximum chamfer axial coordinate completely coincide with each other. Due to the error of the machine tool itself during the processing, it was difficult to ensure that the three points fully met the customer's technical requirements. The technical department modified the processing parameters over and over again based on the test results of the trial processing. The roller workshop readjusted the machine tool, trimmed the grinding wheel and reprocessed it based on the parameters modified by the technical department. After repeated adjustments and repeated tests, the three points finally coincided perfectly, and the processed contour graphics were better than those of peers.

After receiving the production task, the Production Support Department organized the Technical Department, Quality Assurance Department, and Roller Workshop to hold a special meeting to predict the difficulties in the processing process in advance and formulate detailed production plans for tooling, fixtures, and inspection tools. All responsible persons fully cooperated and connected tacitly to overcome many processing difficulties such as the machine tool not being able to move and the insufficient range of the inspection instrument. Finally, the roller successfully passed the customer's acceptance.